cement plant ball mill design data
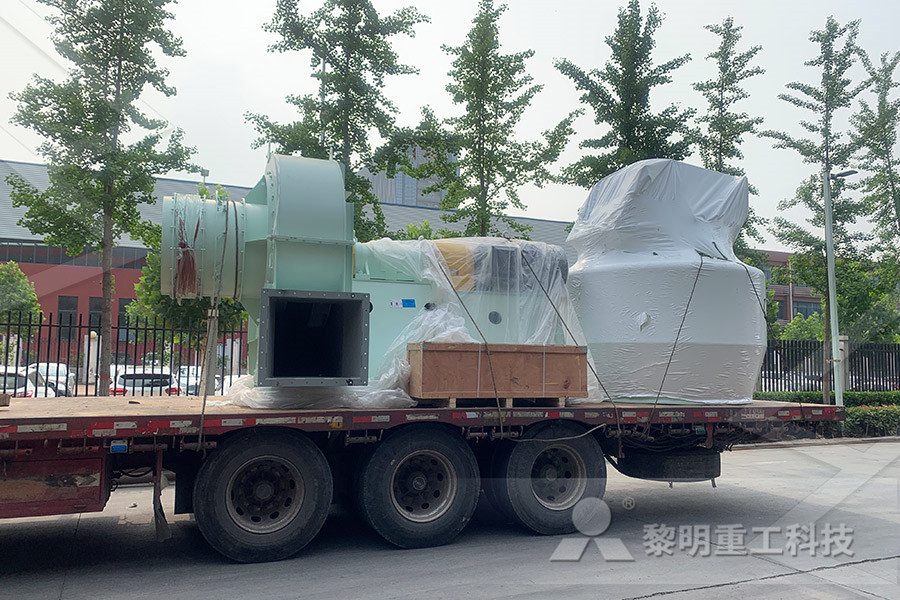
cement plant ball mill design data grinding mill
cement plant ball mill design data grinding mill Ball Mill Roller Press Systems for Cement Grinding The combined grinding system of roller press and ball mill With the invention of Vtype separator, the combined grinding system composed of roller press and ball mill has been developed to further reduce the energy consumption of the cement Cement Ball Mill Design In India nnguniclub cement ball mill design pdf pakistan stone crusher plant cement ball mill design pdf pakistan process crusher The is the professional mining equipments manufacturer in the world, located in China,India, Get Price; Improvements in New FICEM 3 1design of a ball cement mill FelonaAdditional tools required It will increase the plant off time Increasing Man hours and manpower Liner replacement, bolt tightening will be complicated Inlet Chute Design ConsiderationsThe following parameters are considered while designing the mill inlet chute for powdery materials UMS ø46m Cement mill It is the mostly sold mill in FLSDK (PDF) DESIGN AND ANALYSIS OF BALL MILL INLET

Large Ball Mill For Large Scale Mining And Cement
A large ball mill is known for its large processing capacity and long daily operation time, so it is also called a large scale ball mill or large capacity ball mill The large ball mill is especially suitable for largescale grinding production It adopts two bin grinding, which is more energysaving and environmental protection The large scale ball mill adopts the horizontal cylindrical rotating structure, and the appearance design Cement ball mill is widely used in cement production, silicate products, new building materials, refractories, fertilizers, black and nonferrous metal mineral processing, glass, ceramics, and other industries It is the ideal grinding equipment for cement clinker, Use Cement Ball Mill Grinding Cement Clinker The mill is designed to handle a total ball charge of 3245 t at 100% loading with a percentage filling of 295% in both the chambers Both the chambers of the cement mill were charged with 80% of the designed charge, which works out to 86 t in Ist chamber and 172 t in the IInd chamberPROCESS DIAGNOSTIC STUDIES FOR CEMENT MILL

Mono Chamber Raw Mill Ball Charge Design Page 1
The raw material is preground by to a hammer crusher and after separation by a third generation separator the course material is fed to the monochamber raw mill The technical data of the mill is as follows: Mill diameter: 32 m Mill Length: 637 m Effective Mill diameter: 3 m (the mill liners are 95 mm) Effective Mill Length: 6 m Liner: Lifting plates Mill Speed: 17 rpm 3 PROPOSED CEMENT PLANT DESIGN 31 Dynamic Simulation The proposed architecture is a highly automated solution for Cement Process Plant It has been developed on LabVIEW platform software version 2009 The simulated model generates real time process and electrical data and the design is very efficient and user friendly19928645 CEMENT PLANT SIMULATION AND DYNAMIC Plant site and laboratory studies were conducted to collect data for modelling and simulation of the threecompartment ® ball mill Design specifications of the ball mill and applied grinding media size distributions are given in Table 1, Table 2, Table 3Optimization of an industrial scale open circuit three
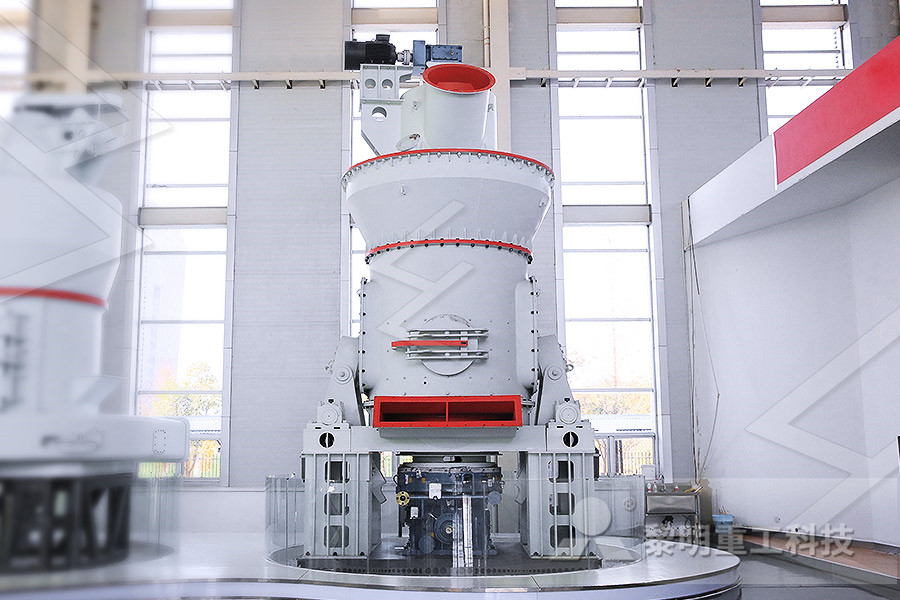
Operational Experience from the United States' First
Their vertical roller cement mill is one of the most modern components of the plant Although the new mill was rated for 130 STPH (118 MTPH), it has operated consistently in the range of 140150 STPH (127 to 136 MTPH) at a product fineness of 39004000 Blaine FIGURE 4 shows the cement mill production both immediately afterAdditional tools required It will increase the plant off time Increasing Man hours and manpower Liner replacement, bolt tightening will be complicated Inlet Chute Design ConsiderationsThe following parameters are considered while designing the mill inlet chute for powdery materials UMS ø46m Cement mill It is the mostly sold mill in FLSDK (PDF) DESIGN AND ANALYSIS OF BALL MILL INLET Medium Chrome Alloyed Ball Mill Liner Plates Application of SAG Mill Liner Our SAG Mill Liner are widely used in the grinding stage for mining industry, cement industry, thermal power plant, papermaking and chemical industry etc Semiautogenous mills or SAG mills, as they are often called, can accomplish the same size reduction work as two or three stages of crushing and screeningMill In Liner Plate Design calculation In cement Plant
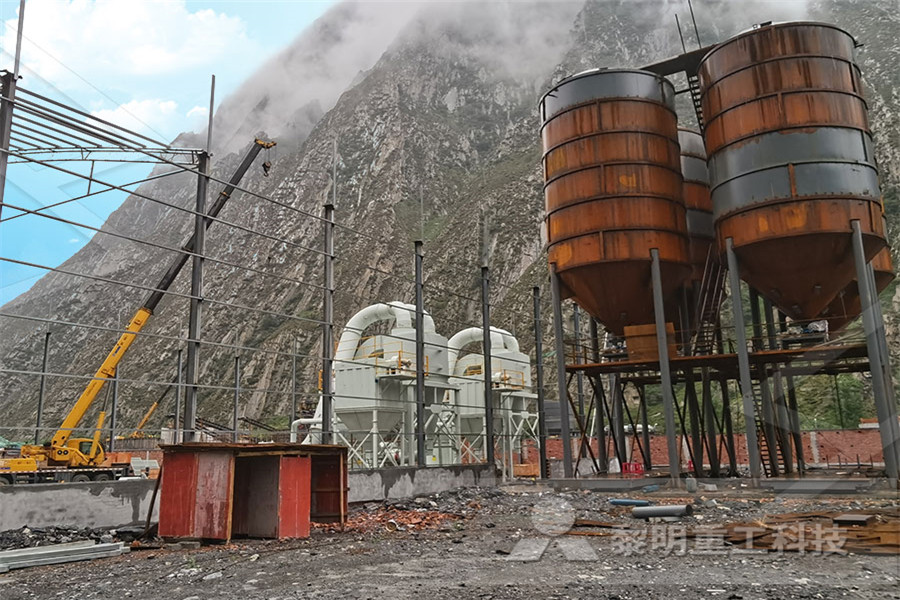
Evolutionary Design of Intelligent Controller for a Cement
mill returns (tailings), z [tons] is the amount of material in the mill (also called the mill load), d represents the clinker hardness, (v) is the separation function and (z,d) is the ball mill outflow rate The grinding function (z,d) is shown in Fig2 for different values of d It is a non monotonic function of the mill 12 Ball MillBall Weight Surface Area 97 13 Ball Mill Charge Volume 98 14 Useful Data for Grinding Mill Study 99 15 Ball Mill Charging 99 16 BIS Specification of Additives 102 17 BIS Specifications for various 103 Cements 18 Thermo Physical Properties of Different Insulating Materials 107 19 Pollution Standards for Stack, Ambient Cement Formulae Green Business Centre 13 By using the model parameters obtained from Plant I data, the size distributions and tonnages for the Plant 11 circuit were predicted The results were verified by the actual data taken from Plant II The measured vs predicted size distributions around the HPGR, ball mill and separator are shown in Figures 14, 15 and 16, respectivelyModelling cement grinding circuits ScienceDirect
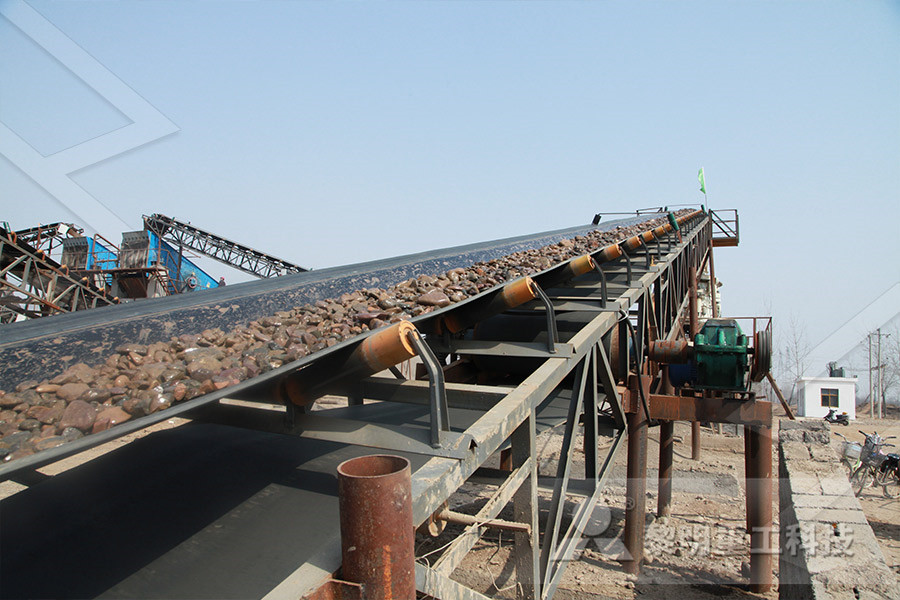
Simulation of clinker grinding circuits of cement plant
GENÇ Ö, BENZER A H Horizontal roller mill (Horomill®) application versus hybrid HPGR/ball milling in finish grinding of cement [J] Minerals Engineering, 2009, 22: 1344–1349 Article Google Scholar [6] LYNCH A J Mineral crushing and grinding circuits, their simulation, optimization, design and control [M] the cement plant Therefore separate or standalone electrical supply equipment will be required Raw material grinding In the raw mill, the material chunks are ground finer to allow highquality blending In this phase mainly vertical mills are used which grind ): Automation solutions for the Cement Industry A case study has been conducted on the wear problem of a set of large helical gears of a ball mill used for cement production at the Shiraz Cement Plant The ball mill has a nominal capacity of 80 t h −1 The overall diameter and length are respectively 4000 mm and 12990 mm The total weight of the ball mill when fully charged is about 280 tWear of gears: A case study at Shiraz Cement Plant

IMPROVED CEMENT QUALITY AND GRINDING
iii ABSTRACT Improved Cement Quality and Grinding Efficiency by Means of Closed Mill Circuit Modeling (December 2007) Gleb Gennadievich Mejeoumov, BS, Ivanovo State Power University, Russia;Cement plant motor manufacturing is one of our main product focuses Cement mills, fans, shredders in the production of cement, particularly large and efficient motors are required for the most diverse processes MENZEL offers individual motor solutions for all applications in the cement Cement plant motors up to 13,8kV and 20000 kWAdditional tools required It will increase the plant off time Increasing Man hours and manpower Liner replacement, bolt tightening will be complicated Inlet Chute Design ConsiderationsThe following parameters are considered while designing the mill inlet chute for powdery materials UMS ø46m Cement mill It is the mostly sold mill in FLSDK (PDF) DESIGN AND ANALYSIS OF BALL MILL INLET

Evolutionary Design of Intelligent Controller for a Cement
mill returns (tailings), z [tons] is the amount of material in the mill (also called the mill load), d represents the clinker hardness, (v) is the separation function and (z,d) is the ball mill outflow rate The grinding function (z,d) is shown in Fig2 for different values of d It is a non monotonic function of the mill 12 Ball MillBall Weight Surface Area 97 13 Ball Mill Charge Volume 98 14 Useful Data for Grinding Mill Study 99 15 Ball Mill Charging 99 16 BIS Specification of Additives 102 17 BIS Specifications for various 103 Cements 18 Thermo Physical Properties of Different Insulating Materials 107 19 Pollution Standards for Stack, Ambient Cement Formulae Green Business Centre 13 By using the model parameters obtained from Plant I data, the size distributions and tonnages for the Plant 11 circuit were predicted The results were verified by the actual data taken from Plant II The measured vs predicted size distributions around the HPGR, ball mill and separator are shown in Figures 14, 15 and 16, respectivelyModelling cement grinding circuits ScienceDirect

): Automation solutions for the Cement Industry
the cement plant Therefore separate or standalone electrical supply equipment will be required Raw material grinding In the raw mill, the material chunks are ground finer to allow highquality blending In this phase mainly vertical mills are used which grind For cement grinding, the highpressure grinding roll (HPGR) POLYCOM ® and the staticdynamic separator SEPOL ® PC can be installed as a finishgrinding circuit or, in combination with a ball mill, as a combigrinding systemHighefficient cement manufacturing with iii ABSTRACT Improved Cement Quality and Grinding Efficiency by Means of Closed Mill Circuit Modeling (December 2007) Gleb Gennadievich Mejeoumov, BS, Ivanovo State Power University, Russia;IMPROVED CEMENT QUALITY AND GRINDING
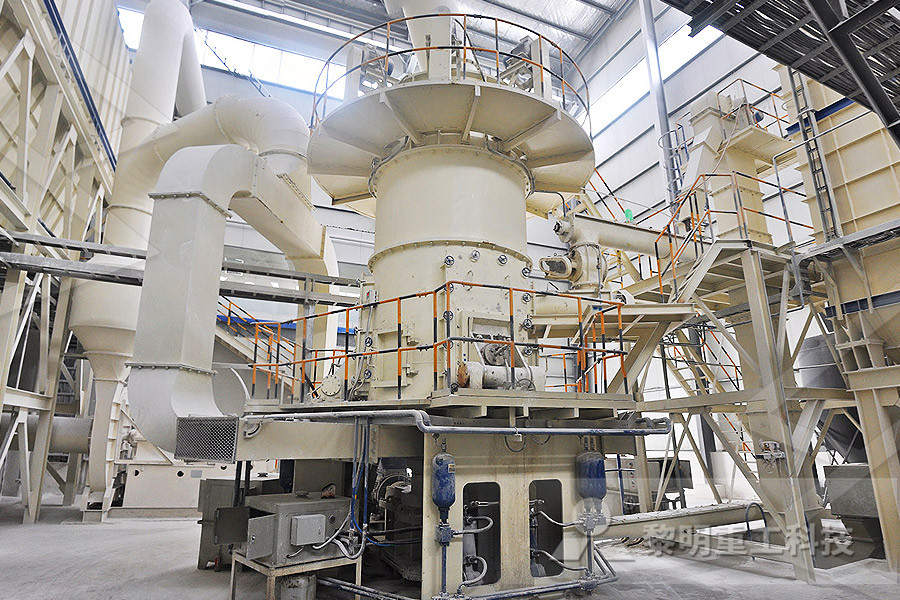
cement plant optimization
online training courses foe cement industry,most updated knowledge of cement manufacturing, online calculators, cement plant optimization, through improvement in energy efficiency, reduce carbon footprint, enhance productivity with sixsigma and lean manufacturing theme, Portland cement plant means any facility manufacturing portland cement Raw material dryer means an impact dryer, drum dryer, paddleequipped rapid dryer, air separator, or other equipment used to reduce the moisture content of feed or other materials Raw mill means a ball and tube mill, vertical roller mill or other size reduction equipment Portland Cement Manufacturing Industry NESHAP According to the data we know, the total cost of a cement plant is estimated to be US$ 75 to US$ 100 per ton One thing to be clear, this is just an estimation, in the real cement plant building, the cement factory cost is affected by various factors, including the significant difference in cost of land, availability of limestone mines, etcHow Much Does It Cost To Start A Cement Plant?